×
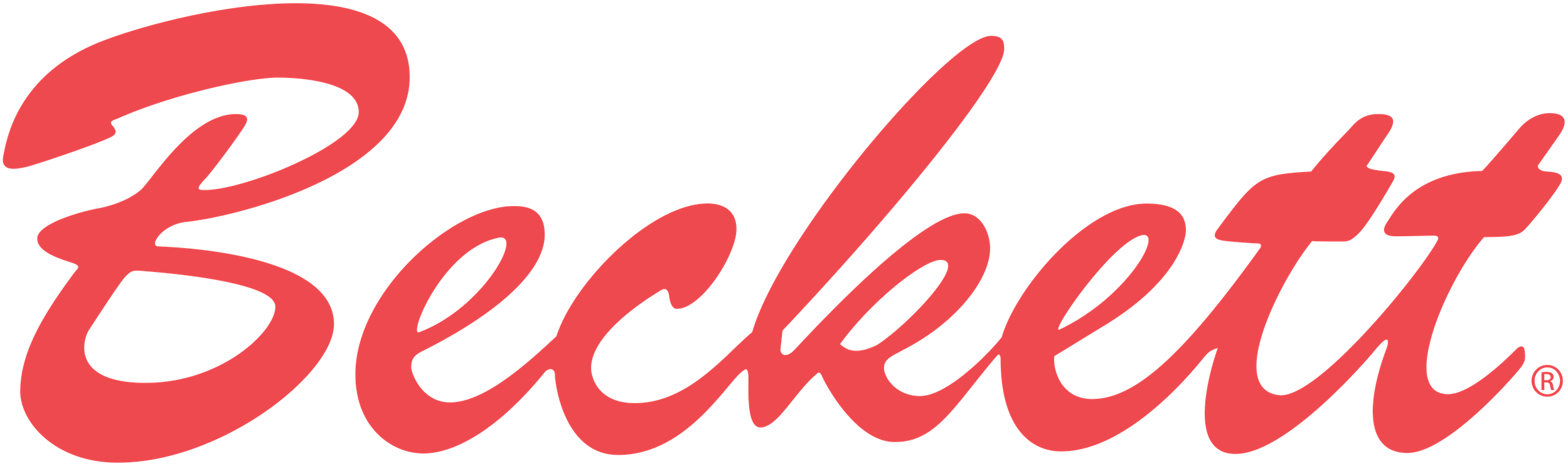
Regional Sales Manager Request
Please fill out the form below to contact Beckett directly and we’ll get back to you within 24 hours.
We get inquiries concerning upgrading old stoker units where the burner can be fired through the upper fire door or lower ash pit door. In this bulletin we will discuss some guidelines that will enable you to make successful retrofit applications in these older units.
Our experience has shown that retrofit can be made successfully, either by firing in the lower grate area, or through the upper feed door. The choice is yours. Use the method that works best for you.
1 Firing Rate (GPH) | 2 Length (L) | 3 Width (W) | 4 Dimension (C) | 5 Suggested Height (H) | 6 Minimum Dia. Vertical Cyl. |
0.50 | 8 | 7 | 4 | 8 | 8 |
0.65 | 8 | 7 | 4.5 | 9 | 8 |
0.75 | 9 | 8 | 4.5 | 9 | 9 |
0.85 | 9 | 8 | 4.5 | 9 | 9 |
1.00 | 10 | 9 | 5 | 10 | 10 |
1.10 | 10 | 9 | 5 | 10 | 10 |
1.25 | 11 | 10 | 5 | 10 | 11 |
1.35 | 12 | 10 | 5 | 10 | 11 |
1.50 | 12 | 11 | 5.5 | 11 | 12 |
1.65 | 12 | 11 | 5.5 | 11 | 13 |
1.75 | 14 | 11 | 5.5 | 11 | 13 |
2.00 | 15 | 12 | 5.5 | 11 | 14 |
2.25 | 16 | 12 | 6 | 12 | 15 |
2.50 | 17 | 13 | 6 | 12 | 16 |
2.75 | 18 | 14 | 6 | 12 | 18 |
Keeping these considerations in mind will help you in your application work. Many experienced contractors have made installations in the manner described here, and they have been able to achieve fine results.
Informative and technical training resources from the leading experts in the heating industry
Have questions about our products? Looking for a solution to address a particular application? Looking to improve the overall productivity and profitability of your operation? Please don’t hesitate to reach out or schedule a no obligation, 1-on-1 consultation with a Beckett Technical Specialist — we’d love to help.
Beckett solutions are available through our network of Distributors, Independent Representatives, and Export Representatives all around the world.